Learn about the 6 inspections procedures used in food packaging, from visual inspection and more. Keep your food safe with these tips!
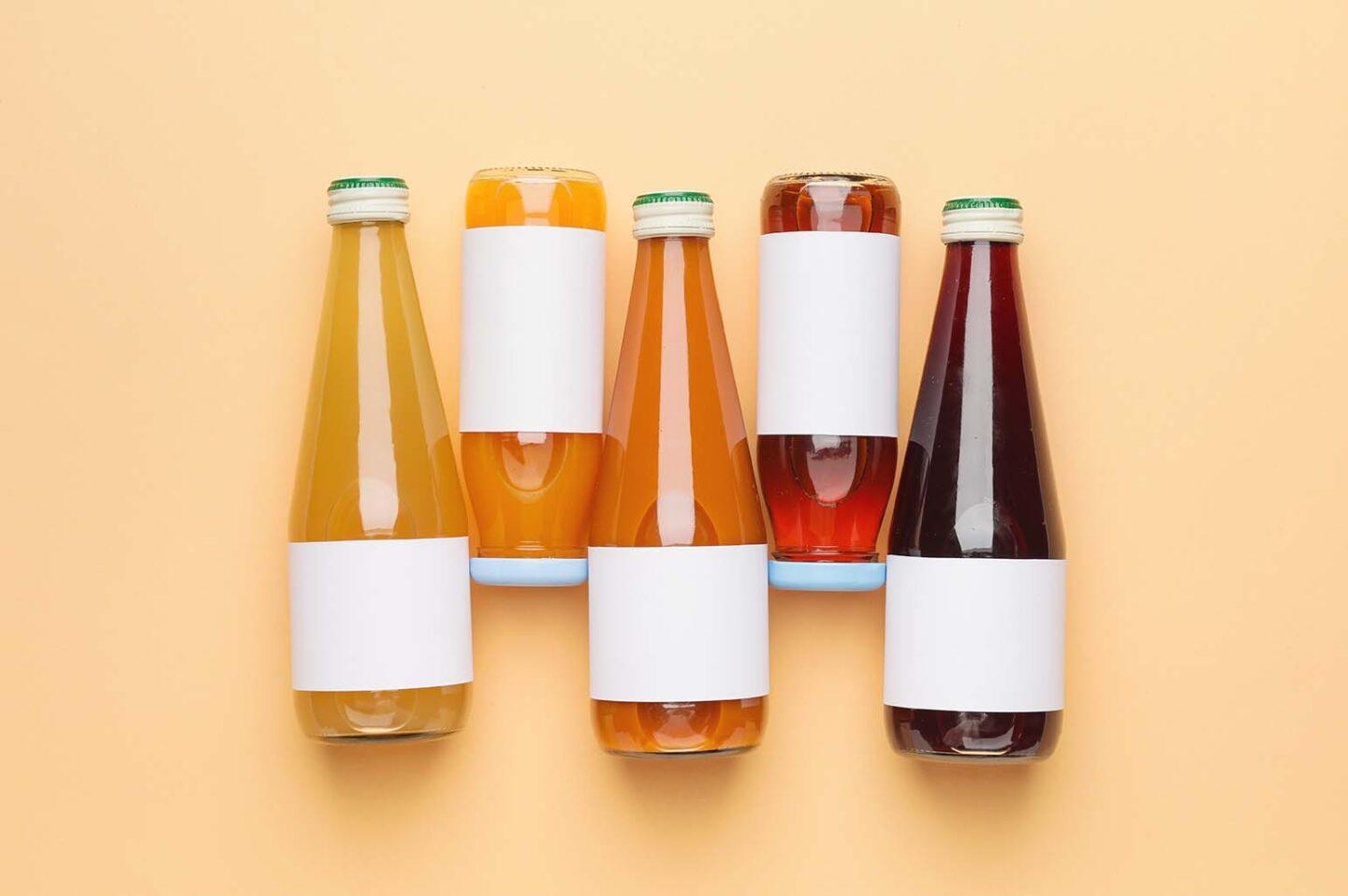
Are you an aspiring food scientist, packaging engineer, quality assurance specialist, or just someone who’s interested in how the food we eat goes from farm to table? If so, learning about the process for inspecting and verifying the safety of packaged foods is a great place to start. With proper inspection procedures and processes in place, consumers can rest assured that their meals are safe from contamination and other hazards. Read on to discover six inspections used in food packaging – they will help you understand why these vital steps must be taken with each product!

Visual inspection
Taking a close look at the products we purchase has never been more important. Visual inspection plays a critical role in ensuring that each item is not only visually appealing but also free of any defects. Whether it’s dented cans or broken seals, these imperfections can be a sign of larger problems that could affect the safety and quality of the product. That’s why taking the time to thoroughly check each item can save us from potential headaches down the line. It’s no longer enough to trust that everything was manufactured to the highest standards. By becoming more vigilant in our visual inspections, we are protecting ourselves and those around us from harm. So the next time you shop, take a moment to give each product a thorough once-over. Your diligence could make all the difference.
Size verification
When it comes to purchasing a product, one of the most important aspects is making sure that it’s the right size and weight. There’s nothing worse than ordering something online, eagerly anticipating its arrival, only to find out that it doesn’t fit or isn’t the weight you were expecting. That’s why size verification is such a crucial step in the buying process. By confirming that the product is the right size and weight, you can ensure that you’re getting exactly what you paid for.
This not only saves you the hassle of having to return the item, but it also saves you time and money in the long run. So before you hit that “buy” button, make sure to take a moment to double-check the size and weight of the product. Trust us, it’s worth it.
Date code verification
Ensuring that these packaged foods are still within their expiration dates is essential for our health and safety. This is where date code verification comes in. It is a process of checking that all the labels on packaged foods have accurate expiration dates. It is important to note that the date code is not just a random number; it is a code that represents specific information like the production date, batch code, and expiration date. Thus, verifying the date code ensures that we consume fresh and safe food.
Imagine how much waste and potential harm we could prevent with this simple yet crucial step in the manufacturing process. So next time you reach for that packaged snack, take a moment to check the date code and ensure that it’s within its expiration date.
X-Ray inspection
Automated X-ray inspection technology has become increasingly popular in the food packaging industry due to its numerous benefits. One of the major advantages is the ability to detect any physical defects or contaminants that may be present in food packaging materials. These defects can include incomplete seals, broken seals, and foreign objects that may pose a risk to the consumer.
By using X-ray inspection technology, it is possible to detect these defects quickly and efficiently, allowing manufacturers to address them before the product is shipped out. This not only helps to maintain the quality of the product but also ensures the safety of the consumer. Additionally, an X-ray for bottles and jars is able to successfully detect defects, making it a versatile solution for the food packaging industry. As a result, it has become a very important tool for ensuring the quality and safety of food packaging.
Leak test
Measuring any leaks or seepage during transport, storage, or distribution is imperative. A leak test is an essential technique employed to check the integrity of a package and its contents. This process determines whether a package’s seals and closures are airtight and leak-free. With this, it is easy to detect any leaks before they cause damage to the product or, worse, pose a safety hazard. So, if you are packaging food, a leak test is a critical quality assurance measure that gives you peace of mind knowing that your products are protected.
Packaging material testing
In the world of product packaging, there is no room for error. From the moment a product leaves the manufacturer to reach the hands of consumers, the packaging must be able to withstand the rigors of transportation, handling, and storage. This is where packaging material testing comes in. By evaluating the strength and durability of packaging materials, manufacturers can ensure that their products arrive intact and in pristine condition.
Furthermore, compliance with regulations is a must, and testing helps to ensure that all packaging materials meet standards and guidelines set by regulatory bodies. With packaging material testing, manufacturers can have peace of mind knowing that their products are well-protected and compliant with regulations.
In Conclusion
When it comes to product packaging, there are several steps that must be taken in order to ensure the safety and quality of your products. From double-checking sizes and weights before purchasing, date code verification for expiration dates, X-ray inspection for physical defects or contaminants, leak tests for airtight seals and closures, and material testing for strength and durability – these processes all play an important role in ensuring a safe and reliable end product.
With thorough attention paid at every stage of the process, from design through production to delivery, you can have peace of mind knowing that your products will reach their destination safely intact. So take the time necessary during each step of the process – after all, it is worth investing in when we think about our health and safety!